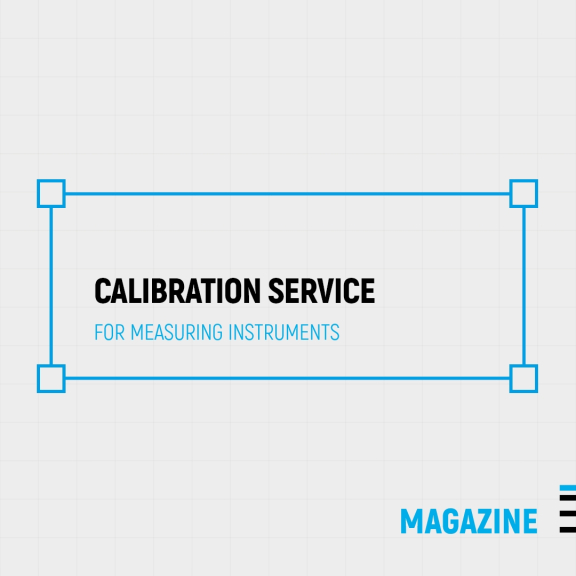
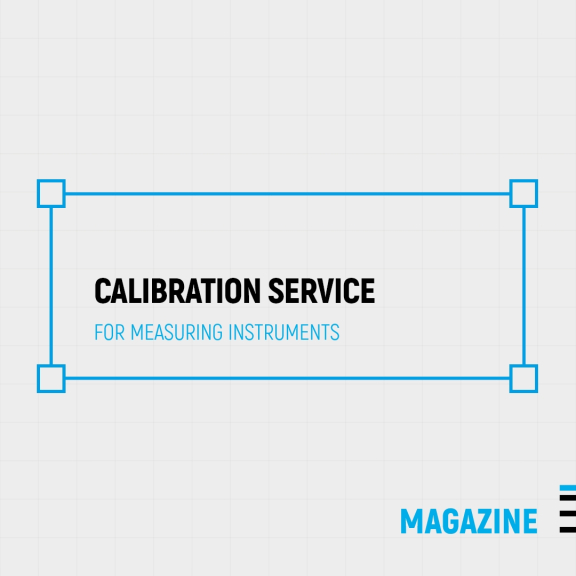
CALIBRATIONS CALIBRATION SERVICE FOR MEASURING INSTRUMENTS
What is meant by calibrating an instrument?
Calibrating a measuring instrument involves determining its metrological conformity within known accuracy limits. This ensures the instrument's ability to measure correctly and repeatably within the calibration interval. This is achieved by comparing the measured values of the instrument under test with those of a more accurate reference instrument, known as the calibration standard. The values from both the instrument being calibrated and the reference instrument, along with the comparison results, are recorded in the calibration certificate.
What is the difference between calibration and adjustment?
Calibration is a service that defines the metrological characteristics of a measuring instrument. It is performed by comparing the instrument with a reference instrument, known as a standard, within a specific time frame defined by the customer or a specific norm. Adjustment, on the other hand, is an operation to "tune" the instrument to make it more accurate. Calibration is not synonymous with "setting" or "fine-tuning" the measurement.
When is calibration required?
According to ISO 9001, all companies must develop a system for controlling calibration. The frequency of calibration can depend on various factors, such as the manufacturer's recommendations, the frequency of use of the instrument, or the conditions of use.
What can be calibrated?
Calibrations are classified according to the metrological area to which the instruments belong. These include physical quantities such as length, pressure, temperature, humidity, force, torque, mass, and electric current; physical properties such as pH value, concentration of a substance, or more complex areas like vehicle speed, ionizing radiation, etc. TECHNE calibrates measuring instruments for the main physical quantities: length, pressure, temperature, humidity, force, torque, mass, and electric current.
How is the calibration of instruments carried out?
As mentioned earlier, the calibration of an instrument is performed by comparison.
However, different equipment may be used depending on the type of instrument being calibrated.
In our laboratories, dimensional calibration (length) is performed using:
Calibrating a measuring instrument involves determining its metrological conformity within known accuracy limits. This ensures the instrument's ability to measure correctly and repeatably within the calibration interval. This is achieved by comparing the measured values of the instrument under test with those of a more accurate reference instrument, known as the calibration standard. The values from both the instrument being calibrated and the reference instrument, along with the comparison results, are recorded in the calibration certificate.
What is the difference between calibration and adjustment?
Calibration is a service that defines the metrological characteristics of a measuring instrument. It is performed by comparing the instrument with a reference instrument, known as a standard, within a specific time frame defined by the customer or a specific norm. Adjustment, on the other hand, is an operation to "tune" the instrument to make it more accurate. Calibration is not synonymous with "setting" or "fine-tuning" the measurement.
When is calibration required?
According to ISO 9001, all companies must develop a system for controlling calibration. The frequency of calibration can depend on various factors, such as the manufacturer's recommendations, the frequency of use of the instrument, or the conditions of use.
What can be calibrated?
Calibrations are classified according to the metrological area to which the instruments belong. These include physical quantities such as length, pressure, temperature, humidity, force, torque, mass, and electric current; physical properties such as pH value, concentration of a substance, or more complex areas like vehicle speed, ionizing radiation, etc. TECHNE calibrates measuring instruments for the main physical quantities: length, pressure, temperature, humidity, force, torque, mass, and electric current.
How is the calibration of instruments carried out?
As mentioned earlier, the calibration of an instrument is performed by comparison.
However, different equipment may be used depending on the type of instrument being calibrated.
In our laboratories, dimensional calibration (length) is performed using:
- Universal measuring bench Mahr ULM600;
- Linear measuring bench ZEUSS 3000 HIGH PRECISION;
- Ceramic-coated parallel gauge blocks of grade 0;
- Set of smooth master rings from Ø3 mm to Ø600 mm.
- Torque testing bench;
- Manual pressure generators;
- Tension and compression testing machine.
- Calibration furnaces;
- Thermostatic baths;
- Calibrators;
- Primary sensors for temperature and humidity;
- Multimeters and climate chambers.